Packaging machine repair service for fixing complex machinery issues.
Packaging machine repair service for fixing complex machinery issues.
Blog Article
Exactly How Professional Product Packaging Machine Repair Service Solutions Lessen Downtime and Increase Efficiency
In today's competitive landscape, the efficiency of product packaging procedures is extremely important for preserving a successful business. Specialist packaging equipment repair work services are crucial in minimizing downtime and boosting efficiency via specialized diagnostics and timely treatments. By applying precautionary upkeep strategies, these services not just avert pricey malfunctions yet also make sure constant product quality and process. The effects of such services prolong past prompt repair services-- unboxing the broader influence on functional efficiency exposes crucial insights into long-term efficiency methods. The inquiry continues to be: how can businesses leverage these services to attain lasting growth?
Significance of Timely Repairs
Prompt fixings of product packaging devices are vital for keeping functional effectiveness in any kind of production setting. When machinery malfunctions or breaks down, it can bring about considerable disturbances in assembly line, causing boosted downtime and lost profits. The longer a product packaging device remains out of commission, the better the influence on general performance, possibly causing hold-ups in meeting orders and diminishing customer contentment.
Along with the immediate monetary effects, postponed repair work can lead to extra considerable damages to the machinery. Components that are not addressed without delay can wear away additionally, needing even more expensive repairs or complete substitutes, which could have been stayed clear of with prompt intervention. Additionally, regular maintenance and timely fixings can boost the lifespan of product packaging equipments, making sure that they operate at optimal performance degrees - packaging machine repair service.
Buying professional product packaging maker repair service solutions is necessary for reducing these dangers. A positive approach to repair services not only keeps production timetables but also cultivates a culture of dependability within the organization. By focusing on timely repair services, businesses can keep their competitive edge, maximize resource allocation, and inevitably enhance their bottom line via enhanced functional effectiveness.
Experience in Diagnostics
When it pertains to preserving the efficiency of product packaging equipments, experience in diagnostics plays a crucial duty in recognizing issues prior to they intensify into significant failings. Proficient specialists use sophisticated diagnostic devices and strategies to do complete evaluations of maker efficiency. This aggressive method allows them to pinpoint the origin of malfunctions, whether they originate from mechanical wear, electric faults, or software discrepancies.
Effective diagnostics not only help with swift identification of issues yet also boost the overall reliability of product packaging operations. By conducting thorough assessments, technicians can assess the health and wellness of essential elements, guaranteeing that even minor abnormalities are resolved immediately. This focus to detail reduces the danger of unanticipated failures, which can bring about pricey downtime.
Moreover, professional diagnostics supply important understandings right into functional patterns, allowing companies to make educated decisions regarding tools upgrades or modifications. By leveraging these understandings, firms can maximize their packaging processes, causing improved efficiency and efficiency. Ultimately, buying diagnostic knowledge is crucial for companies seeking to preserve seamless operations and support high requirements of top quality in their packaging processes.
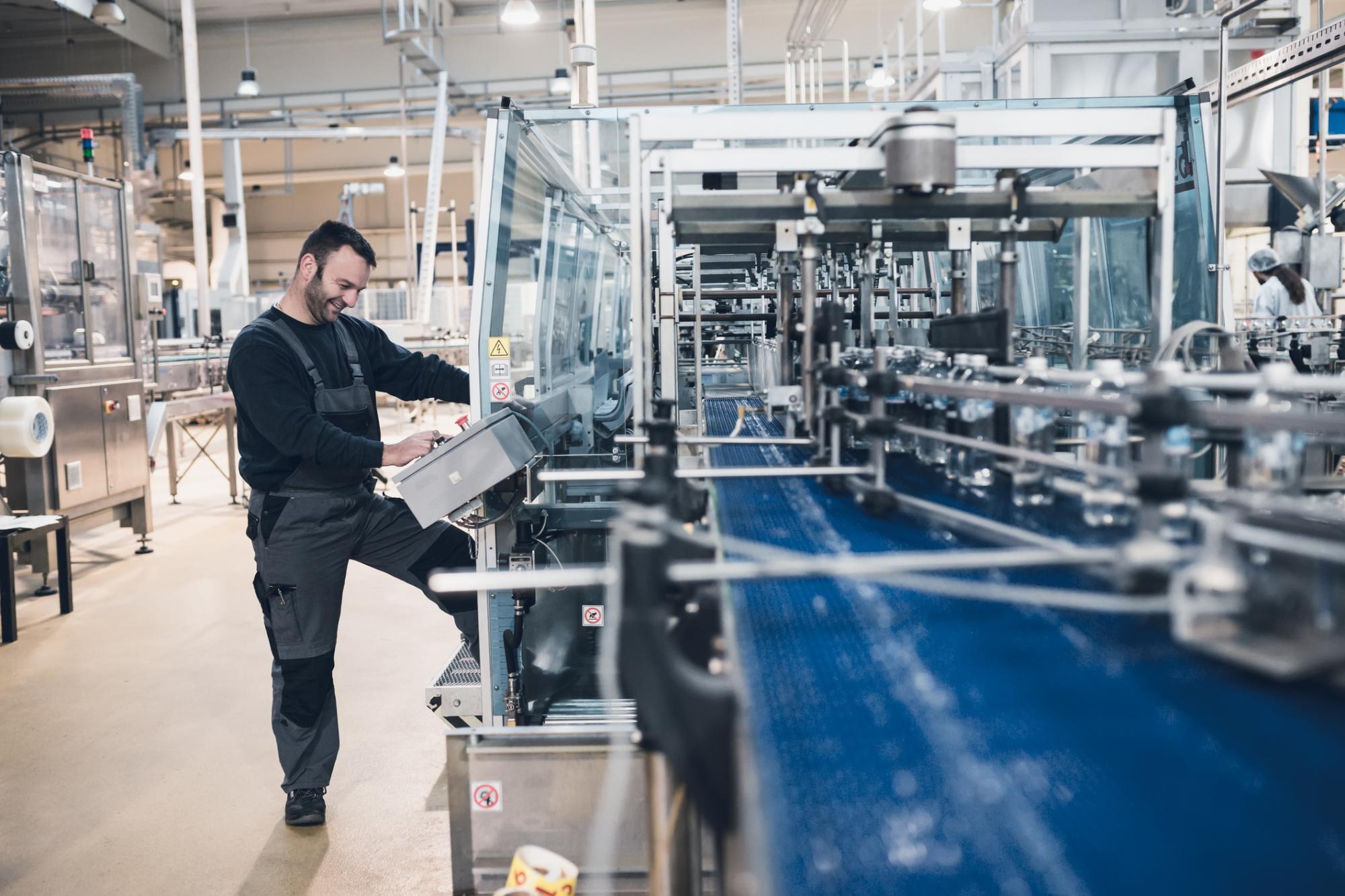
Preventive Maintenance Advantages
Preventive upkeep complements professional diagnostics by proactively dealing with possible issues prior to they manifest into significant troubles. By applying an organized preventative maintenance program, companies can substantially decrease the risk of unexpected maker failures, therefore navigate here reducing pricey downtime. Regular inspections, cleaning, and parts replacement assistance ensure that product packaging machinery runs at optimum efficiency.
Among the crucial advantages of preventive maintenance is its capability to expand the life expectancy of devices. By on a regular basis keeping machinery, businesses can avoid the worsening results of damage that usually result in significant repair services or replacements. This not only saves funding however likewise improves the general integrity of production processes.
Furthermore, preventative maintenance adds to enhanced safety problems within the work environment. By recognizing and fixing potential risks before they rise, companies produce a more secure setting for their staff members (packaging machine repair service). This positive strategy not only safeguards workers yet also fosters a culture of responsibility and vigilance
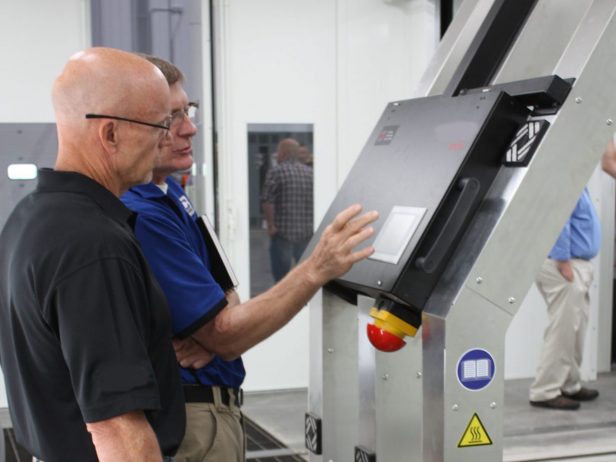
Custom-made Service Solutions
Identifying the unique needs of each service, personalized service options for packaging device repair offer tailored methods that improve operational performance. These options are developed to attend to particular difficulties dealt with by different markets, making certain that equipment downtime is decreased and efficiency is maximized.
Professional repair service solutions begin with a detailed analysis of a company's product packaging operations. By understanding the certain machinery included and the needs of the production setting, technicians can establish a customized repair and maintenance plan. This might consist of specialized training for internal staff, the execution of anticipating maintenance innovations, or the arrangement of specialized assistance during optimal manufacturing times.
In addition, customized services can integrate flexible service arrangements that straighten with a business's operational routine, permitting repair services to be carried out throughout off-peak hours. By focusing on my company the distinct needs of each service, these custom options make sure that fixings are not only effective however likewise perfectly integrate right into existing process.
Eventually, the emphasis on personalization enables firms to enhance their packaging procedures, leading to improved integrity and performance of machinery, which is essential for keeping competitive advantage in today's fast-paced market.
Effect on General Effectiveness
Customized service solutions not just address certain fixing demands yet additionally play a considerable duty in improving overall operational performance. By providing targeted interventions, expert packaging maker repair work services directly lower the regularity and period of tools failings. This aggressive method makes certain that production lines stay operational, decreasing disruptions that can lead to costly downtime.
Additionally, reliable fixing services contribute to smoother workflows, as well-kept equipment operates at ideal efficiency degrees. When equipments work properly, the quality of packaged items improves, causing fewer flaws and much less rework. This enhancement not just boosts productivity however likewise strengthens client satisfaction.
Additionally, routine upkeep and quick response times from fixing experts foster a society of integrity within the organization. Workers can focus on their key jobs instead of fretting regarding prospective tools break downs. The general throughput of the manufacturing process increases, permitting firms to fulfill need extra properly.
Inevitably, the strategic investment in specialist repair service solutions translates to enhanced performance across all operational elements, ensuring that businesses can adjust and flourish in an open market. This synergy between upkeep and efficiency is important for lasting success.
Conclusion
To conclude, expert product packaging equipment fixing solutions play a vital role in minimizing downtime and boosting efficiency within manufacturing settings. Prompt fixings, specialist diagnostics, and precautionary upkeep contribute to the integrity of devices, while personalized solution remedies attend to specific functional demands. The cumulative effect of these services results in improved total performance, making it possible for services to preserve production routines, copyright item top quality, and efficiently satisfy market demands. Purchasing such solutions ultimately drives continual operational success (packaging machine repair service).
Report this page